Alternatively, if you want to detect a water leak in your home, you can check your water usage. If it has gone up significantly without reason, then this could be a leak. You can also take a meter reading and wait two hours ensuring not to use any water and take another meter reading. If your usage has increased, this indicates a leak.


If you need a 24hr Emergency Boiler repair or a leaking or kitchen sink tap repair then call today and we can arrange for one of our Plumbers or boiler Gas Engineers in Stevenage to help you!
All our boiler repair and service engineers are gas safe registered. If you need a Local plumber near you we can help with over 35 years in the trade.
Should I bother servicing my boiler?
Boiler Repairs from Abbotts Maintenance provides boiler repair servicing to customers in SG1, SG2 & Stevenage. Our boiler repair & service response time can be within the hour, with 95% of boiler repairs completed within the first hour. All gas central heating boilers can Benefit from regular servicing. Did you know that regular boiler servicing helps your central heating system work at peak performance throughout the year, especially during the cold winter months? Avoid costly boiler repairs at the worst time of year by booking boiler service.
If you need a 24hr Emergency Boiler repair or a leaking or kitchen sink tap repair then call today and we can arrange for one of our Plumbers or boiler Gas Engineers in Stevenage SG1 SG2 to help you!
All our boiler repair and service engineers are gas safe registered. If you need a Local plumber near you we can help with over 35 years in the trade.
Emergency Boiler Repairs Stevenage
Should I bother servicing my boiler or repairing a boiler?
Abbotts Maintenance Boiler servicing & repair in Stevenage is essential since the colder climate requires frequent use of boilers during the winter months and sometimes, even during the summers. Using a faulty boiler is not only dangerous, but can significantly contribute to increased utility bills.
A boiler that is not functioning to standards specified by the manufacturer can cause gas leaks that are dangerous for both the occupant as well as neighbours. There is also the danger of carbon monoxide poisoning, which can be prevented by regular servicing of your boiler.
Why does a boiler need repair or servicing?
As with any other appliance, regular use of a boiler will lead to decreased efficiency and deterioration over a period of time. This occurs for two main reasons: as the boiler is used, excessive soot, which is a by-product of the combustion process, can coat the inside components of the boiler leading to reduced efficiency, and the air-to-fuel ratio, which needs to be maintained for optimum performance, changes over a period of time due to component wear and tear. Boiler repairs & servicing is particularly important, since the boiler is being used daily almost throughout the year.
Abbotts Maintenance entails a service that will come to your home, clean the soot from your boiler and ensure that the air-to-fuel ratio is readjusted to optimize efficient running of your appliance. This will prolong the life of your boiler and will reduce the risk of expensive repairs in the long run.
Another critical reason to carry out proper maintenance on your boiler, is to prevent exposure to carbon monoxide, which, when inhaled over a period of time can lead to illness and even death. Incomplete combustion of fuels such as oil or gas in infrequently serviced boilers can lead to the production of carbon monoxide.
This gas is odourless and colourless and therefore hard to detect. Regular servicing can alert you to the presence of carbon monoxide and help keep you and your family safe.
Who will service my boiler and what qualifications should I check for?
At Abbotts Maintenance Stevenage boiler repairs are carried out by a service engineer or technician who is specifically qualified to work on your particular type of boiler. All qualified service technicians should be Gas Safe Registered, all our engineers are. This is a certification that ensures that the engineer has been adequately trained to service your appliance from both a legal as well as a safety stand point.
Every Gas Safe registered engineer will have a Gas Safe identification card that will specify the company name and contact details, the engineers license number, whether he is qualified to work on domestic or commercial applications and his area of expertise – gas, LPG or oil boilers and other appliances.
There are several online services that allow you to check the credentials of the technician prior to permitting him to work on your boiler. Even though a registered technician might be more expensive, it is well worth the additional expense to ensure that the repair is carried out in a safe and professional manner, thereby preventing more problems in the future.
When and how often should I get my boiler serviced?
Abbotts Maintenance recommend servicing your boiler annually to ensure that it is running smoothly and to carry out any repairs that might be required in a timely manner.
By doing this potential problems can be detected early and repaired before they lead to bigger problems. It is recommended that regular servicing be carried out in the summer months, when boiler engineers are readily available so that the boiler is functioning well during the cold winter months when you will need to use it regularly.
Make sure you ask your technician for any safety tips; most technicians will also give you advice on how to maintain your boiler for superior performance and longevity.
What will the boiler engineer do when he arrives for the service?
The first task a technician will perform is a visual check to ensure that the running, fixing and positioning of the boiler complies with laws relating to installation, building codes, electrical, water and gas regulations laid out in the current legislation.
Next, the technician will fire up the unit to ensure that it is running properly and check for any faults before he opens the casing. Once the casing is opened, your service technician will check all the components of the boiler including the electrical parts, pipes, joints and interior surfaces for damage. He will also clean the inside surfaces of the boiler and readjust the air-to-fuel ratio to optimum values. If there are any faults, he will inform you of additional costs to repair or replace any parts.
Before replacing the boiler casing, he will carry out tests to ensure that there are no gas leaks. The entire process should take between 30-60 minutes, at the end of which you should receive a service report stating what checks and servicing the technician has performed.
Radiator Problems, Not Heating or as Hot?
Have a radiator that needs repairing, installing or moving? We regularly undertake all kinds of radiator work from issues with a lack of heat being produced, leaks from the connecting pipe work and re-fitting radiators that have parted from the wall. For a radiator not heating as it should could be due to rust- sludge in the central heating system and this will need power flushing.
Have you got a Leaking or Burst Pipe.
Water leaking from a fractured or burst pipe can cause extensive damage to your property if prompt action is not taken. That is why our fully qualified engineers are available to provide an emergency response in Abbots Langley , arriving on site to trace the source and resolve the problem as quickly as possible, ensuring that water damage is kept to a minimum. All of our plumbers are highly qualified and fully insured and all of the work they completed is fully guaranteed.
We offer an expert service, so call Abbotts Maintenance you can be sure of a local, fast and quality service. Call us now!
Is your Leaking Tap driving you crazy.
Did you know that on average a leaking tap can lose up to 90 litres of water per week, costing you money and damaging the environment by increasing the amount of water that needs to be extracted from natural sites? We work on all kinds of tap whether it be mono bloc, mixer or conventional we can offer a complete repair in the majority of cases, limiting the money that the leaking water can cost you. In cases where a repair is not possible we can provide and install a new tap or fit a tap provided by you.
Do you have a Leaking Bath or Shower Tray.
Unfortunately in many cases a leaking bath or shower tray can only be identified once water damage begins to appear directly below the bathroom. But don’t worry, our specialist engineers can be on site within two hours to trace the source of the leak and repair the problem, limiting any further damage to your property.
Problem with your Shower not working.
Shower leaking or suffering from low water pressure?
There is nothing more frustrating than not being able to wash properly so give us a call and we can have an engineer onsite within two hours on average. You’ll be back to steaming hot, invigorating showers before you know it!
Is you Water Tank Leaking.
Water tanks are often sited in inaccessible locations within properties meaning that it can be difficult to identify an issue with the tank until the damage resulting from the problem becomes visible. A hidden leaking or overflowing water tank can be very destructive so we offer a priority service to our customers to prevent further damage to their property or belongings.
Need a new Appliance Fitted or Removed.
New washing machine, dishwasher or fridge freezer need fitting? We can make any necessary adaptations to existing plumbing to ensure that the new appliance fits and functions as it should and we can be with you within two hours on average or at an agreed time that suits you better.
Toilet Leaking or a Sticking Ball valve.
A leaking toilet can be an annoying problem to have, particularly if it is for public use on a commercial premises. That is why we carry out repairs to toilets and urinals in domestic, office, public houses and restaurants to ensure that the facility is fully working again as soon as possible and with the minimum of fuss. Do you find you have a noisy toilet after flushing? this is due to a poor ballvalve in need of changing.
Common Error codes.
Common fault codes on Worcester Bosch boiler range from EA 227 to E9. Vaillaint gas boilers have fault code like F75 low water to F26, F29 lack of gas or problems within the boiler. Baxi E119 low water E133 lack of gas.
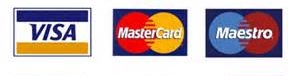
Frequently Asked Pumbing & Heating Question
Emergency Plumbers & Boiler Repairs
Perhaps something most homes have encountered is the drip, drip, drip from a tap.
This can happen for a variety of reasons such as general wear and tear, a build up of debris
or when someone doesn’t turn the tap tight enough. It can even leak if someone over-tightens the
valve as it can lead to damage to the washer in the tap.
If you have a leaking tap, then it is wise to inspect the tap to determine the cause. Firstly,
switch off the water supply through an isolator valve or the stopcock. Then if you feel comfortable to do so,
open up the tap and inspect the washer.
You may notice that it has a build-up of debris which you can clean away.
Alternatively, the washer may have damage, and it is time for a replacement.
Only replace the washer if you feel comfortable to do so. If you don’t,
a competent handyman or plumber will be happy to assist.
Another common water leak is through a leaking radiator. A leaking radiator can cause significant damage to your floor,
ceiling and even wiring, so it is vital to fix it right away.
A water leak in the radiator could be from a number of different causes such as a leaking valve or valve spindle. Alternatively,
it may be leaking because of corrosion or pipe coupling.
Most of the fixes for a leaking radiator will require draining the system and refilling it. Furthermore,
the components of a radiator are relatively fiddly and can be difficult to master. For a leak in the radiator, determine where you think the leak is coming from,
then turn off your water supply and then it is usually best to call a plumber to resolve the issue for you.
If you spot a leak from a plastic/PVC water pipe joint, then the good news is that you may be able to fix the issue yourself. Remember, water can travel a long way before it drips as a leak, so you need to make sure you know exactly which joint the leak is coming from. Start by drying the area thoroughly and working out exactly where the water is coming from and whether it is the pipe or water pipe joint that is leaking.
Once you know the source of the leak, turn off the water for the affected area, or turn off the water at the mains supply if that is easiest.
Then get to work in fixing a leak. If you feel competent, remove and replace the affected section of the pipe. However, this may require cutting tools and equipment you may not have. Alternatively, you can make an easy temporary fix using rubber or silicone repair tape which is quick and easy to use. Repair epoxy can be even easier to use around plastic water pipe joint leaks, and it can mould to fit the shape of the joint.
If you have a leaking plastic water pipe, then the process is much the same as how to fix a leaking plastic water pipe joint. First make sure you know exactly where the leak is coming from, turn off the water supply and then either replace the affected water pipe or use a quick fix such as tape and epoxy.
Alternatively, for a super quick fix, you can use a rubber and hose clamp to give you some time before you can call a plumber out to make the fix.
Vaillant boiler problems and fault codes
Mass flow sensor not connected/disconnected,
plug not connected or incorrectly connected or an issue with its operation.
Mass flow sensor faulty, filter below venturi filter cap wet or blocked, gas flow pressure too low.
No or too little gas supply pressure, gas valve closed.
Mass flow sensor not connected/disconnected,
plug not connected or incorrectly connected or an issue with its operation.
Interruption/short circuit of water pressure sensor, interruption/short circuit to GND in supply line to water pressure sensor or water pressure sensor defective.
Water pressure sensor and/or pump defective, air in heating installation, too low water pressure in boiler; check adjustable bypass, connect external expansion vessel to return.
Ideal Logic, Icos & Isar Boiler fault Codes
The problem
If your heating system doesn’t have enough water, this fault can occur as its pressure could become low.
The solution
It is usually possible for you to fix this issue yourself by topping up your boiler’s water pressure to 1.5 using the in-built in filling loop. If you’re still facing issues, contact a Gas Safe registered engineer.
The problem
This usually means that there has been a flame loss during operation. This issue could be caused by deeper system errors such as incorrect gas pressure, an issue with your flue, a faulty gas valve, an incorrect adjustment of a valve or a fan fault.
The solution
Firstly, check other gas appliances and you could try to reset your boiler. This fault typically occurs with older boilers and low-efficiency systems, so it may be worth considering getting a new boiler installed.
The problem
This fault is caused by a loose or damaged fan. This issue could be related to deeper problems such as loose or damaged connections, water damage from a boiler leak, a fault with the air pressure switch or a problem with the printed circuit board.
The solution
This fault will require the help of a qualified engineer. As the issue can stem from a range of different causes, costs can vary.
The problem
The F4 fault code tends to signify a problem with your boiler’s flow thermistor or an issue with its operation. The fault will typically be related to circulation issues.
The solution
This fault will require a call out to a Gas Safe registered engineer.
The problem
This refers to a fault in the return thermistor or its operation. related to a faulty NTC return thermistor, a damaged connection, a differential in temperature that’s too high between the flow/return thermistors, or a faulty printed circuit board.
The solution
This fault will require a call out to a Gas Safe registered engineer.
The problem
Your boiler takes resistance readings which are then sent to the printed circuit board and if the temperature reading is too low or too high, the boiler will cease to work as a safety precaution and display a fault code.
The solution
Reset your boiler. If this doesn’t help, you should then contact a qualified engineer. Overheating is generally an issue that happens with older, less efficient boilers, so it may be worth investing in a new heating system.
The problem
Your boiler has ‘locked out’ as a safety precaution. The cause behind this will need to be identified.
The solution
Reset your boiler. If there’s rumbling coming from the system, this suggests your condensate pipe is blocked or that there is an issue with your flue. This requires a call out from a qualified engineer.
The problem
This fault code typically indicates that someone has changed the printed circuit board (PCB) and used the wrong boiler chip card (BCC).
The solution
This requires a call out from a qualified engineer.
The problem
Like L1, this code could indicate that the temperature on your resistance reading is too high.
The solution
Check your system’s pressure reading, you could also bleed your radiators to see if this helps. If not, we recommend contacting a Gas Safe registered engineers as the overheating could be a result of a deeper issue with your boiler’s pump or dry fire stat.
The problem
Your boiler may have ‘locked out’ as a safety precaution. The cause of this will need to be addressed.
The solution
Check that other gas appliances in your home are working, if so, we recommend that you then reset your boiler. If your boiler is rumbling, there could be a blockage in your condensate pipe. Contact a qualified engineer to fix the issue.
The problem
This could occur if someone may have reset the boiler 5 times in 15 minutes.
The solution
Turn off the boiler’s power at the fuse spur, then turn it back on again. If the issue continues, contact a qualified engineer.
The problem
This usually happens when your flame comes on before your gas.
The solution
Reset your boiler. If the boiler still fails to operate and your system is still covered by your warranty, you could contact your manufacturer for assistance.
Perhaps something most homes have encountered is the drip, drip, drip from a tap. This can happen for a variety of reasons such as general wear and tear, a build up of debris or when someone doesn’t turn the tap tight enough. It can even leak if someone over-tightens the valve as it can lead to damage to the washer in the tap. If you have a leaking tap, then it is wise to inspect the tap to determine the cause. Firstly, switch off the water supply through an isolator valve or the stopcock. Then if you feel comfortable to do so, open up the tap and inspect the washer. You may notice that it has a build-up of debris which you can clean away. Alternatively, the washer may have damage, and it is time for a replacement. Only replace the washer if you feel comfortable to do so. If you don’t, a competent handyman or plumber will be happy to assist.
Another common water leak is through a leaking radiator. A leaking radiator can cause significant damage to your floor, ceiling and even wiring, so it is vital to fix it right away. A water leak in the radiator could be from a number of different causes such as a leaking valve or valve spindle. Alternatively, it may be leaking because of corrosion or pipe coupling. Most of the fixes for a leaking radiator will require draining the system and refilling it. Furthermore, the components of a radiator are relatively fiddly and can be difficult to master. For a leak in the radiator, determine where you think the leak is coming from, then turn off your water supply and then it is usually best to call a plumber to resolve the issue for you.
If you spot a leak from a plastic/PVC water pipe joint, then the good news is that you may be able to fix the issue yourself. Remember, water can travel a long way before it drips as a leak, so you need to make sure you know exactly which joint the leak is coming from. Start by drying the area thoroughly and working out exactly where the water is coming from and whether it is the pipe or water pipe joint that is leaking. Once you know the source of the leak, turn off the water for the affected area, or turn off the water at the mains supply if that is easiest. Then get to work in fixing a leak. If you feel competent, remove and replace the affected section of the pipe. However, this may require cutting tools and equipment you may not have. Alternatively, you can make an easy temporary fix using rubber or silicone repair tape which is quick and easy to use. Repair epoxy can be even easier to use around plastic water pipe joint leaks, and it can mould to fit the shape of the joint.
If you have a leaking plastic water pipe, then the process is much the same as how to fix a leaking plastic water pipe joint. First make sure you know exactly where the leak is coming from, turn off the water supply and then either replace the affected water pipe or use a quick fix such as tape and epoxy. Alternatively, for a super quick fix, you can use a rubber and hose clamp to give you some time before you can call a plumber out to make the fix.
Mass flow sensor not connected/disconnected, plug not connected or incorrectly connected or an issue with its operation.
Mass flow sensor faulty, filter below venturi filter cap wet or blocked, gas flow pressure too low.
No or too little gas supply pressure, gas valve closed.
Mass flow sensor not connected/disconnected, plug not connected or incorrectly connected or an issue with its operation.
Interruption/short circuit of water pressure sensor, interruption/short circuit to GND in supply line to water pressure sensor or water pressure sensor defective.
Water pressure sensor and/or pump defective, air in heating installation, too low water pressure in boiler; check adjustable bypass, connect external expansion vessel to return.
The problem If your heating system doesn’t have enough water, this fault can occur as its pressure could become low. The solution It is usually possible for you to fix this issue yourself by topping up your boiler’s water pressure to 1.5 using the in-built in filling loop. If you’re still facing issues, contact a Gas Safe registered engineer.
The problem This usually means that there has been a flame loss during operation. This issue could be caused by deeper system errors such as incorrect gas pressure, an issue with your flue, a faulty gas valve, an incorrect adjustment of a valve or a fan fault. The solution Firstly, check other gas appliances and you could try to reset your boiler. This fault typically occurs with older boilers and low-efficiency systems, so it may be worth considering getting a new boiler installed.
The problem This fault is caused by a loose or damaged fan. This issue could be related to deeper problems such as loose or damaged connections, water damage from a boiler leak, a fault with the air pressure switch or a problem with the printed circuit board. The solution This fault will require the help of a qualified engineer. As the issue can stem from a range of different causes, costs can vary.
The problem The F4 fault code tends to signify a problem with your boiler’s flow thermistor or an issue with its operation. The fault will typically be related to circulation issues. The solution This fault will require a call out to a Gas Safe registered engineer.
The problem This refers to a fault in the return thermistor or its operation. related to a faulty NTC return thermistor, a damaged connection, a differential in temperature that’s too high between the flow/return thermistors, or a faulty printed circuit board. The solution This fault will require a call out to a Gas Safe registered engineer.
The problem Your boiler takes resistance readings which are then sent to the printed circuit board and if the temperature reading is too low or too high, the boiler will cease to work as a safety precaution and display a fault code. The solution Reset your boiler. If this doesn’t help, you should then contact a qualified engineer. Overheating is generally an issue that happens with older, less efficient boilers, so it may be worth investing in a new heating system.
The problem Your boiler has ‘locked out’ as a safety precaution. The cause behind this will need to be identified. The solution Reset your boiler. If there’s rumbling coming from the system, this suggests your condensate pipe is blocked or that there is an issue with your flue. This requires a call out from a qualified engineer.
The problem This fault code typically indicates that someone has changed the printed circuit board (PCB) and used the wrong boiler chip card (BCC). The solution This requires a call out from a qualified engineer.
The problem Like L1, this code could indicate that the temperature on your resistance reading is too high. The solution Check your system’s pressure reading, you could also bleed your radiators to see if this helps. If not, we recommend contacting a Gas Safe registered engineers as the overheating could be a result of a deeper issue with your boiler’s pump or dry fire stat.
The problem Your boiler may have ‘locked out’ as a safety precaution. The cause of this will need to be addressed. The solution Check that other gas appliances in your home are working, if so, we recommend that you then reset your boiler. If your boiler is rumbling, there could be a blockage in your condensate pipe. Contact a qualified engineer to fix the issue.
The problem This could occur if someone may have reset the boiler 5 times in 15 minutes. The solution Turn off the boiler’s power at the fuse spur, then turn it back on again. If the issue continues, contact a qualified engineer.
The problem This usually happens when your flame comes on before your gas. The solution Reset your boiler. If the boiler still fails to operate and your system is still covered by your warranty, you could contact your manufacturer for assistance.
Worcester Bosch Errors fault codes:
Cause code: 362
Reset type: Reset button
Possible cause: Incorrect HCM fitted
Cause code: 233
Reset type: Reset button
Possible cause: Problem with the code plug (faulty or not connected)
Cause code: 222
Reset type: Reset button
Possible cause: Flow sensor shorted or damaged
Cause code: 223
Reset type: Reset button
Possible cause: Flow sensor disconnected or damaged
Cause code: 218
Reset type: Reset button
Possible cause: Primary flow sensor overheated
Cause code: 332
Reset type: Reset button
Possible cause: Primary flow sensor overheated
Cause code: 219 Cause code: 220 Cause code: 221 Cause code: 224
Reset type: Reset button
Possible cause: The main heat exchanger has overheated. Maximum temperature 105°C
Maximum temperature sensor on the main heat exchanger has failed
Maximum temperature sensor on the main heat exchanger has not been recognised
Flue gas thermostat overheat
No flame detected after ignition Cause code: 227
Reset type: Reset button
Possible cause: Failure of four ignition attempts. The boiler waits 30 seconds before another attempt is made
Loss of flame signal during operation Cause code: 229
Reset type: Reset button
Possible cause: An established flame has been extinguished. This could be caused by: – Moisture in the sump, due to a blocked sump/condensate trap – A strong wind into the flue
Gas valve error Cause code: 234
Reset type: Reset button
Possible cause: Gas valve coil disconnected
Ignition timing error
Cause code: 261
Reset type: Reset button
Possible cause: Flame not established during the first 4 seconds ignition period
Abbotts Maintenance - local 24 hour Emergency Boiler Repairs & Boiler Servicing in Stevenage
All of our service engineers are highly qualified and fully insured and all of the work they completed is fully guaranteed. We offer an expert service, so call our Abbotts Maintenance Team ™ today and you can be sure of a local, fast and quality service.
Call us now on 0208 387 0155
✔ Central heating installations
✔ Underfloor heating repairs
✔ Leaking radiator valves
✔ Emergency Plumbers
✔ Leaking toilets
✔ Boiler service & maintenance
✔ Boiler breakdowns
✔ Local Plumbers
✔ Leaking boilers
✔ Leaking washing machines
✔ Leaking dishwashers
✔ Gas engineers
✔ Radiators
✔ Boiler installation
✔ Boiler replacement
✔ Boiler servicing
✔ Thermostats
✔ Gas valves
✔ Circuit boards
✔ Drainage & waste pipe
✔ Blocked manholes
✔ Blocked drains
✔ Blocked toilets
✔ Blocked sinks
✔ Sani flo, Saniflo
✔ WC’s,
✔ Sinks
✔ Immersions
✔ Immersion Heaters
✔ Cylinders
✔ unvented cylinder
✔ Megaflo
✔ Sinks & Sani- Vite
✔ Shower repairs
✔ Electric showers
✔ Power Showers
✔ WC Cistern’s
✔ Syphon
✔ Boiler installations
✔ Boiler repairs
✔ Emergency plumbing
✔ Power flushing
✔ Corgi plumbers
✔ Emergency boiler repairs
✔ Gas safety
✔ Landlord certificates
✔ Gas safety checks
✔ Leaks, Burst pipes
✔ Outside taps
✔ Taps
✔ Cold water tanks
✔ Bathroom refurbishments
✔ Kitchen installations
✔ General Plumber Repairs
✔ Disabled bathrooms
✔ Disabled WC
✔ Fall heating systems
✔ WD3,
✔ WD4,
✔ WD5,
✔ WD6,
✔ WD7,
✔ WD17,
✔ WD18,
✔ WD19,
✔ WD23,
✔ WD24,
✔ WD25,
✔ HP1,
✔ HP2,
✔ HP3,
✔ Al1,
✔ Al2,
✔ AL3,
✔ AL4
✔ AL5,
✔ AL6,
✔ AL7,
✔ AL8,
✔ AL9,
✔ AL10,
✔ SG1,
✔ SG2,
✔ NN14,
✔ NN10,
✔ NN9,
✔ NN8,
✔ NN3,
Rickmansworth,
Chorleywood,
Croxley Green,
Mill End,
Maple Cross,
Batchworth,
Kings Langley,
Chipperfield,
Chaulden
Dacorum,
Abbots Langley,
Bedmond,
Boxmoor
St Albans,
Borehamwood,
Elstree,
Well End,
Hertsmere,
Radlett,
Shenley,
Watford,
Hemel Hempstead,
Hatfield,
Cassiobury,
Bennetts End,
West Watford,
Earls Barton.
Rushden,
Irthlingborough,
Kettering,
Wellingborough,
Kings Langley,
Oxhey,
South Oxhey,
Apsley
Bushey,
Bushey Heath,
North Watford,
Haprenden,
Berkhampsted,
Garston,
Leavesden,
Leverstock Green
Aldenham,
Welwyn Graden City,
Welwyn,
Knebworth,
Stevenage,